When the pandemic hit and borders all over the country were closed during the first lockdown last year, one could only imagine the logistical nightmare that businesses had to deal with to ensure that they could still reach their customers and secure employees’ jobs. Even huge corporations, such as Coca-Cola Beverages Philippines, Inc. (CCBPI)—the bottling arm of Coca-Cola in the country—felt the heat, with the company’s large-scale operations thrown into disarray by the lockdown.
“We employ 10,000 associates spread across the country in our 20 plants and over 70 distribution centers in the Philippines. In terms of our fleet, we own over 3,000 trucks and 2,000 sales service vehicles—so it’s easy to imagine how challenging it was to face an unprecedented crisis like COVID-19,” says Gareth McGeown, president and CEO of CCBPI.
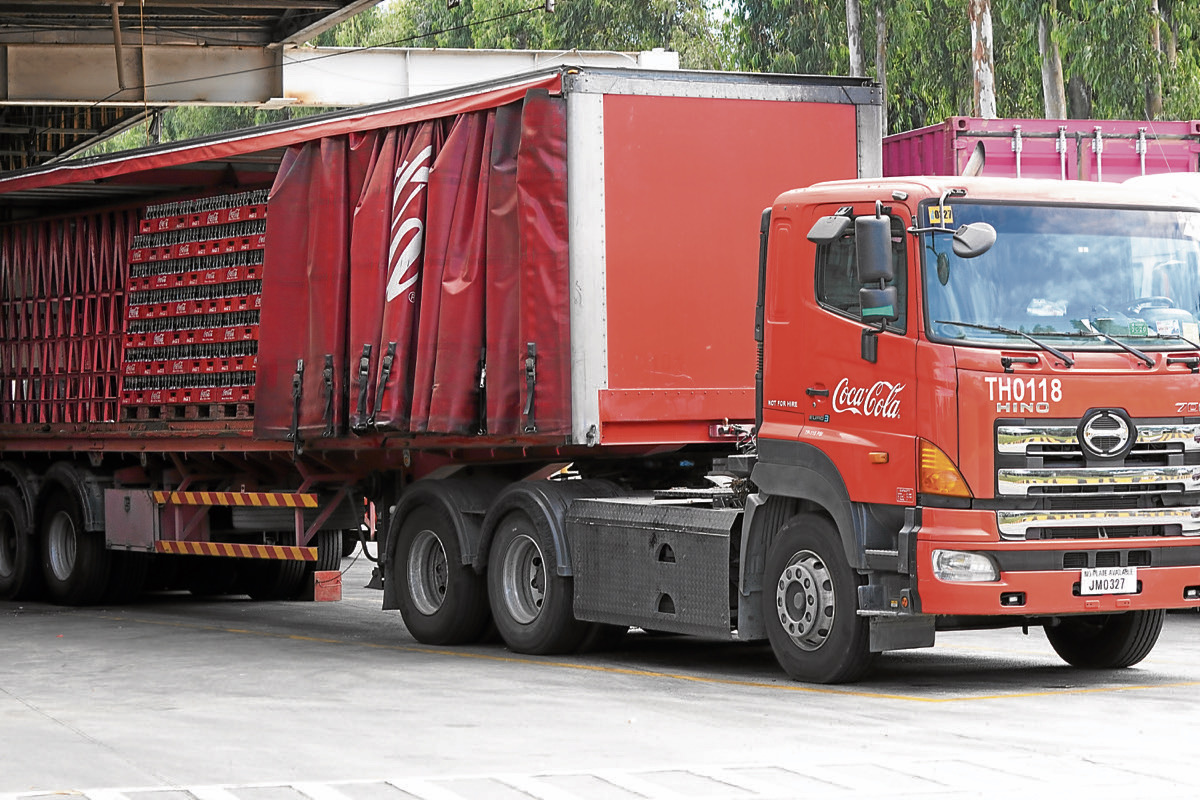
With such large-scale operations, CCBPI manages one of the biggest truck fleets not just in the Philippines, but also within Southeast Asia – totaling close to 3,000 trucks and more than 2,000 sales service vehicles. Approximately 2,500 shipments per day are undertaken, transporting to 20,000 doors across the country.
CCBPI’s experience operating in an archipelago, however, has proved to be an advantage amid the pandemic. Despite challenges encountered over the years, the company has been able to significantly improve in terms of logistics efficiency. CCBPI achieves this, says McGeown, mainly through key initiatives such as Network Optimization, which makes use of simulation tools that allow the company to implement detailed, effective, and efficient logistical plans.
Network optimization
The first level of optimization is the infrastructure master plan level, wherein CCBPI defines plant and distribution center capacity networks. Through this, it is also able to identify inefficient transportation legs, decentralize the sourcing of products and determine economic distance for its beverage products.
At the second level of optimization is the analysis of the distribution network vis-a-vis customer location. “We use this to determine new delivery points and strategies,” explains McGeown.
Finally, the third stage of optimization is related to the last mile network, wherein CCBPI maps out the locations of customers, distributors and company facilities to gain better understanding of how it can further streamline distribution from end to end.
A manifestation of the Network Optimization initiative is Coca-Cola’s Mega Manila Hub. Inaugurated in June 2021, the hub was established in partnership with Container Bridge Philippines, Inc. and Manila North Harbor Point, Inc., and is a strategic convergence point for the company’s shipping operations—allowing for synergized transport movements and improved cost savings to serve even more individuals all over the Philippines.
“The site is our first mega hub in the country, and it is a milestone in our 109-year journey with Filipinos,” says McGeown.
CCBPI’s focus on serving Filipinos goes hand-in-hand with its commitment to sustainability—an integral part of the company’s distribution operations. Thirty percent of its truck fleet are Euro IV-V compliant to ensure cleaner emissions as it transports to approximately 20,000 doors across the Philippines on a daily basis.
These initiatives are all guided by the company’s “People First” philosophy, or its commitment to protecting every associate and supporting its customers and communities.
Supply chain excellence
A testament to this commitment is the provision of upskilling programs for its Supply Chain associates—equipping them to transform with the changing times, as well as boosting their careers in the manufacturing industry. An example is CCBPI’s SMART (Self-Managed, Agile and Reliable Teams) Supply Chain program, wherein associates hired as line producers are supplied with an extensive learning program—allowing them to become the company’s very own production engineers and enabling employees to become part of a highly skilled and agile workforce. It is also focused on supporting CCBPI’s 2025 Growth Ambition through improved productivity and efficiency, labor relations and people engagement.
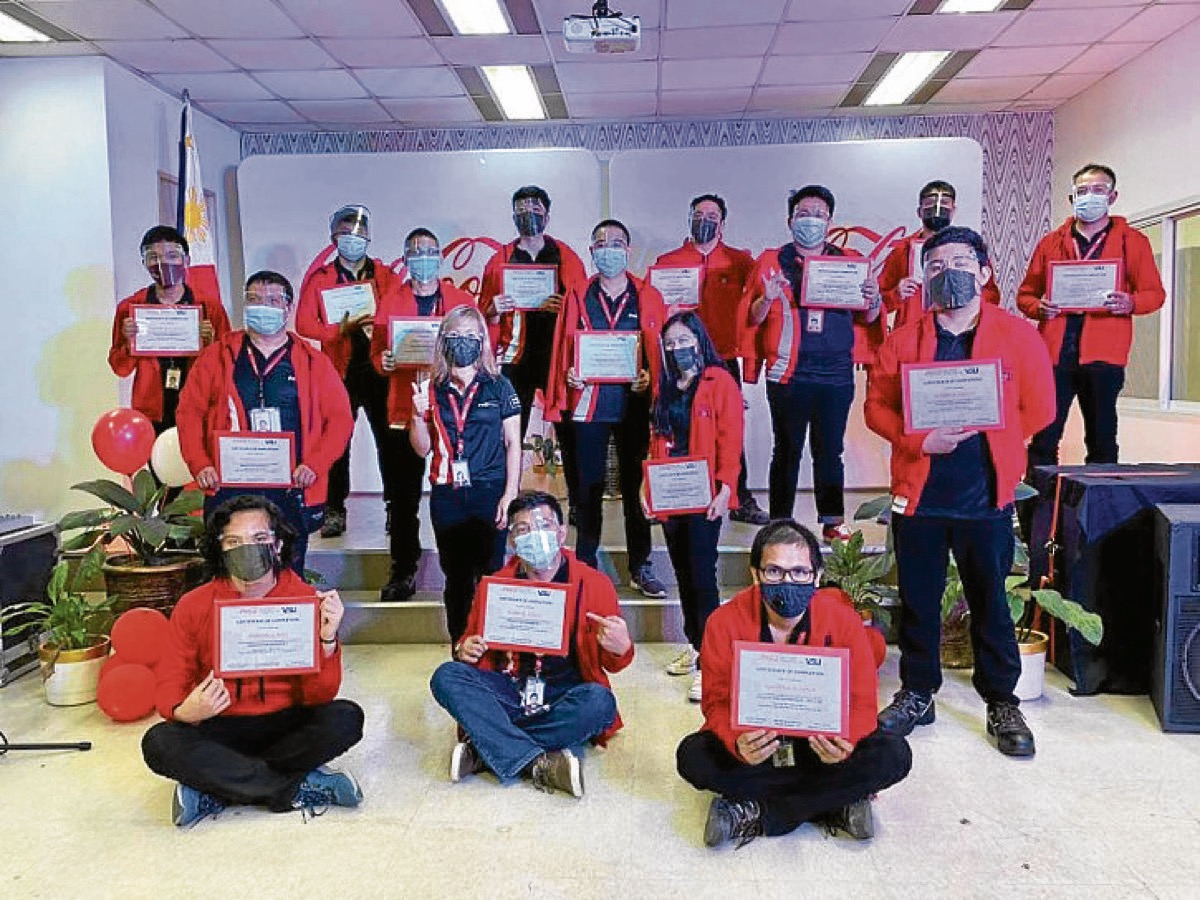
This 2021, 15 Supply Chain representatives from our Davao 2 Plant in Sta. Cruz successfully obtained their Production Engineer 1 certifications – undergoing a rigorous certification process involving exams, License-to-Operate validations, and several revalidas. Training and upskilling are ongoing for more batches of associates from our Manufacturing and Logistics teams to produce our next graduates of SMART Supply Chain.
“It is our responsibility to make sure that all our associates can grow within Coca-Cola. As such, we are changing the way career paths are charted within the company— and how any associate can advance, with the help of the SMART program,” says Gerry Canarejo, director for supply chain excellence of CCBPI.
To further cultivate CCBPI employees’ leadership capabilities, the company also provides:
• A Diploma Program in Supply Chain Management, a six-module training course in partnership with the Philippine Institute for Supply Management, the country’s premier professional association of supply management practitioners;
• A Logistics Management Program, an intensive 3-level training course filled with learning exercises, workshops and coaching—culminating in capstone projects for managers;
• The Lean Six Sigma Green Belt Certificate Program, a 6-month intensive certification training program involving lectures, project implementation, oneon-one coaching and revalida sessions
“These are just some of CCBPI’s many programs that ensure no employee gets left behind,” says Canarejo.
This is the same level of engagement that CCBPI gives to consumers, especially as the Philippines is still facing trying times.
The Coca-Cola System redirected P150 million of its marketing expenses towards the provision of aid to thousands of Filipinos weathering the COVID-19 pandemic and subsequent quarantine measures. Since 2020, CCBPI has donated over 2.2 million liters of drinks to more than 1,500 front-line institutions across the country, provided more than 174,000 personal protective equipment to 350 hospitals and distributed food packs to over 65,000 families.
“We have also been working closely with LGUs (local government units) and NGOs (nongovernmental organizations) to identify critical areas and widen the reach of our efforts,” says McGeown. “Given our operational capabilities and the scale of our truck fleet, it was crucial that we tap all the resources at our disposal and mobilize our organization to provide COVID-19-related relief aid to as many Filipinos as possible.”
From city centers to farflung villages, Coca-Cola employees have been carrying out provision of relief while strictly following safety protocols during operations and deliveries.
Furthermore, in Camalig, Albay, CCBPI and the Coca-Cola Foundation Philippines also deployed the SETA Machine, a transportable water purification unit—so potable water could be made available for the community that was ravaged by Typhoon “Rolly.”
“Through all these Network Optimization and People First efforts, we have been able to deliver solid results and improved customer service.,” says McGeown. “And in 2021, we continue to emerge stronger as a business and as an organization.”